Marshall Multispread provides farmers with a cost effective method of
spreading a range of granulated and non-granulated fertilisers with a
single machine. Traditionally such spreader design could achieve fertiliser
spreading widths of up to 28 m for granulated materials such as Urea and Superphosphate [1].
In general, incremental improvements in the spreader operating performance
can be achieved by a large number of physical tests. However, physical testing
is labour intensive, uses considerable amounts of fertiliser and also introduces
complex variables such as wind speed and direction and particle breakage, which are
difficult to isolate and understand in a physical environment. As a result a numerical
model that could carry out 'virtual' spread tests was developed and then
validated against physical test data and high speed photography.
Design optimisation of Marshall fertilizer spreader
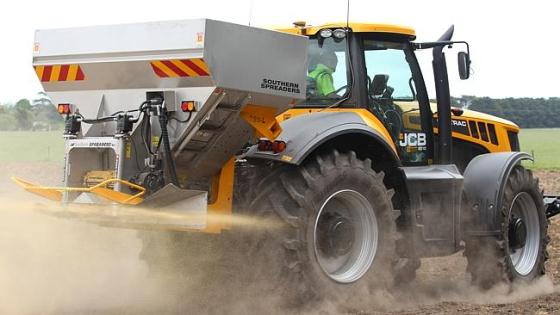
Field fertilizer spreading operation
The objective of the developed modelling procedure was to create a computational tool that would allow
fast assessment of different spreader designs in order to maximize the particle
range and to obtain more uniform fertilizer pattern distribution [2].
In general, particle behaviour can be divided into two stages: calculation of particle motion as they are loaded on the spinner, captured by the spinner vane and accelerated toward the disc periphery, and prediction of particle trajectory as they travel through the air with subsequent determination of their landing position on the ground relative to the spreader centreline.
In general, particle behaviour can be divided into two stages: calculation of particle motion as they are loaded on the spinner, captured by the spinner vane and accelerated toward the disc periphery, and prediction of particle trajectory as they travel through the air with subsequent determination of their landing position on the ground relative to the spreader centreline.
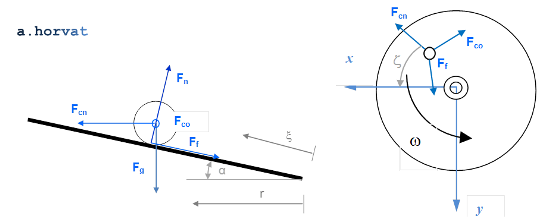
Particle body diagram in absence of guide vanes
Particle motion on the spinner disc is governed by the centrifugal acceleration, where the angular velocity
and the radial position relative to the spinner centreline determine the total kinetic energy
available to the fertiliser particle. On the spinner disc, the motion of a particle in the form of
sliding and rolling is further influenced by friction and Coriolis forces.
Travelling through the air, the particle motion is subjected to aerodynamic drag and gravity forces. Buoyancy and lift forces are considered small in this case and have therefore been neglected.
Travelling through the air, the particle motion is subjected to aerodynamic drag and gravity forces. Buoyancy and lift forces are considered small in this case and have therefore been neglected.
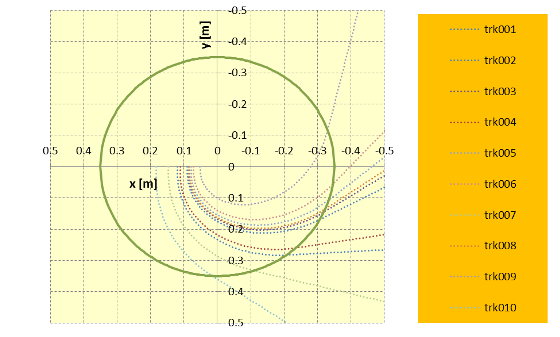
Particle tracks near the spreader
Particle trajectory plots were used to determine how the material properties and loading parameters
influence the particle velocity, angle and their ground lending position. Furthermore, particle deposition
on the ground surface was calculated for typical field parameters. Its linear distribution was directly compared with
the physical tests to validate the modelling procedure.
Such validated numerical model allowed optimisation of the Marshall spreader design in order to increase the particle range
and to achieve more uniform fertilizer coverage of the surface area.
References
- R. Waring, A. Horvat, M. Roesner, Simulation Driven Design Improvement of the Marshall Multispread Fertiliser Spreader, Proceedings, 2013 Society for Engineering in Agriculture (SEAg) Conference, Sept. 22-25, 2013, Mandurah, West Australia.
- A. Horvat, Analysis of Agricultural Spreader Systems, Intelligent Fluid Solutions, Report IFS/R2379, Feb 2011.
Dr Andrei Horvat
M.Sc. Mechanical Eng.
Ph.D. Nuclear Eng.
phone
+44 79 72 17 27 00
skype
a.horvat
e-mail
mail@caspus.co.uk
M.Sc. Mechanical Eng.
Ph.D. Nuclear Eng.
phone
+44 79 72 17 27 00
skype
a.horvat
mail@caspus.co.uk